The following is the full-process technical specification of Guanou New Materials for commercial space wood veneer panel projects, focusing on core principles and technical key points.
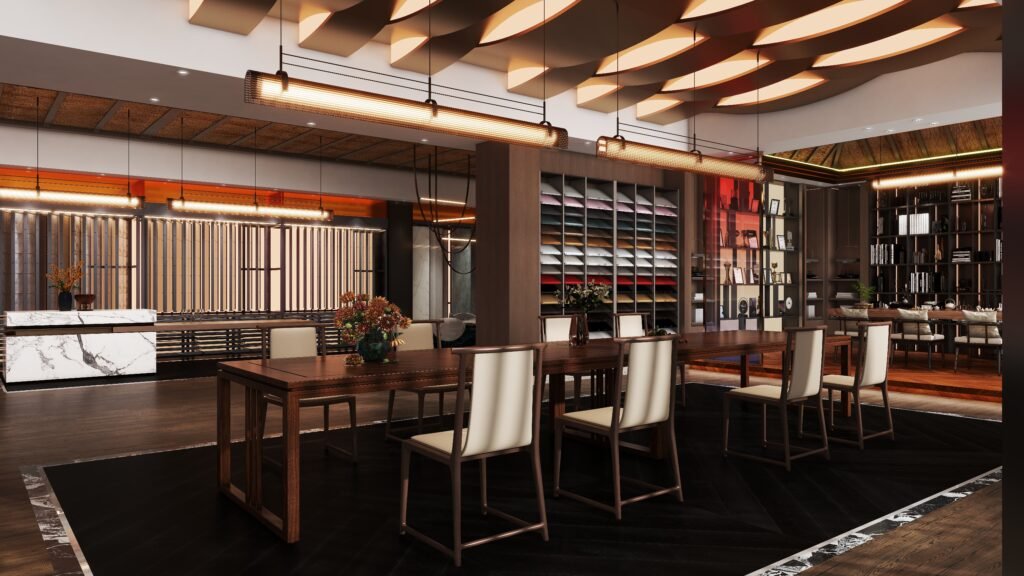
I. Material Selection Specifications
Fire resistance performance is the primary principle for material selection in commercial Spaces. In densely populated areas, decorative panels with A combustion performance of grade A (non-combustible) must be used, while in regular areas, the minimum requirement is Grade B1 (difficult to ignite). The materials should be provided with a combustion performance classification report issued by a national-level testing institution, and key parameters such as the oxygen index and smoke density should be verified.
The physical properties should meet the high-load requirements of commercial environments: the surface wear resistance should be no less than 400 revolutions, the impact strength should be ≥9kJ/m², and the thickness tolerance should be controlled within ±0.2mm. The formaldehyde emission must comply with the ENF grade standard (≤0.024mg/m³), and formaldehyde-free adhesive base materials should be given priority.
II. Standards for Grassroots Treatment
All installation bases must meet the dual conditions of structural stability and environmental adaptability:
The moisture content of the concrete wall should be ≤8%, the flatness error should be ≤3mm/2m, and the cracks need to be filled and reinforced with epoxy resin.
The light steel keel partition wall should be covered with double-layer 12mm gypsum board, the keel spacing should be no more than 400mm, and the cavity should be filled with sound insulation rock wool.
The base surface must be coated with a moisture-proof sealing primer to form an effective moisture-proof barrier.
III. Installation Process Requirements
A composite process combining adhesive bonding and mechanical fixation:
Bonding construction: Use two-component polyurethane structural adhesive, apply evenly with a serrated scraper (≥300g/m²), and ensure that the open time and curing speed match the environmental temperature and humidity.
Mechanical reinforcement: Fixed with stainless steel mosquito nails. The distance between the nails and the edge should be no more than 150mm, and the distance between the nails and the middle should be no more than 300mm. The nail heads should be submerged in the board surface by 0.5mm.
Joint control: Reserve a 0.5mm expansion joint and fill it with high-elasticity silicone sealant (displacement capacity ≥25%) to prevent cracking caused by temperature deformation.
IV. Handling of Key Nodes
Expansion joint setting: When the continuous surface length exceeds 8m, a 10mm-wide through joint should be set and filled with flexible sealing material.
Bevel corner process: 45° bevel cutting and splicing corners or custom profile finishing are adopted, and anti-cracking grooves are opened on the back to release stress.
Equipment interfaces: Structural reinforcement is required at the opening positions of lamps, air outlets, etc. The edge of the hole should be no less than 50mm away from the edge of the plate.
V. Quality Acceptance Criteria
The acceptance process must strictly implement the triple control:
Visual quality: The surface is free of scratches and contamination, the texture is continuous and natural, and the height difference of the seams is ≤0.3mm.
Installation accuracy: Wall flatness ≤1.5mm/2m, squareness error of corners ≤2mm;
Performance verification: On-site sampling and testing of combustion performance and environmental protection indicators, and verification of consistency with the reported inspection materials.
VI. Maintenance and Management Mechanism
Establish a preventive maintenance system:
On a daily basis, electrostatic precipitator maintenance is adopted, and organic solvents are strictly prohibited for cleaning.
The elastic recovery rate of the joint sealant is inspected every quarter. If it is lower than 80%, the joint needs to be re-filled.
The effectiveness of the fireproof coating is evaluated annually. When the residual flame retardant content is less than 70% of the factory value, supplementary treatment is carried out.
Major damages should be dealt with at different levels according to the contingency plan. If the damage exceeds 10cm, the entire board must be replaced and the maintenance record should be filed.
VII. Key Points of Project Management
Detailed design: Complete the approval of the layout drawing of the decorative panel and the detailed drawing of the nodes before construction to avoid on-site cutting.
Process traceability: Each board is affixed with a unique identification code, which is associated with the entire process information of production, transportation and installation.
Team certification: Construction personnel must hold professional installation qualifications, and special operation positions require additional assessment.
This specification ensures that commercial wood veneer projects meet the industry high standards of safety and durability, visual refinement, and controllable maintenance through four core dimensions: material performance control, process standardization, acceptance data, and management traceability. The above is the full-process technical specification for tooling by Guanou New Materials, focusing on core principles and technical key points. If you want to know more details, you can contact me.
